VISI Flow
VISI Flow die rheologische Analyse
Die Anwendung von VISI Flow erfordert keine physikalischen oder mathematischen Kenntnisse. Ein Grundwissen für Werkzeugdesign und Spritzgießen ist ausreichend, um die Anfangsbedingungen festzulegen und die Ergebnisse zu interpretieren. Die verfügbare Hilfestellung bei der Eingabe und bei der Interpretation der Ergebnisse, verbunden mit dem intuitiven Interface und der praxisorientierten Sprache, erleichtern die Anwendung. Folgt man den vorhandenen Beispielen, so beherrscht man VISI Flow innerhalb weniger Tage.
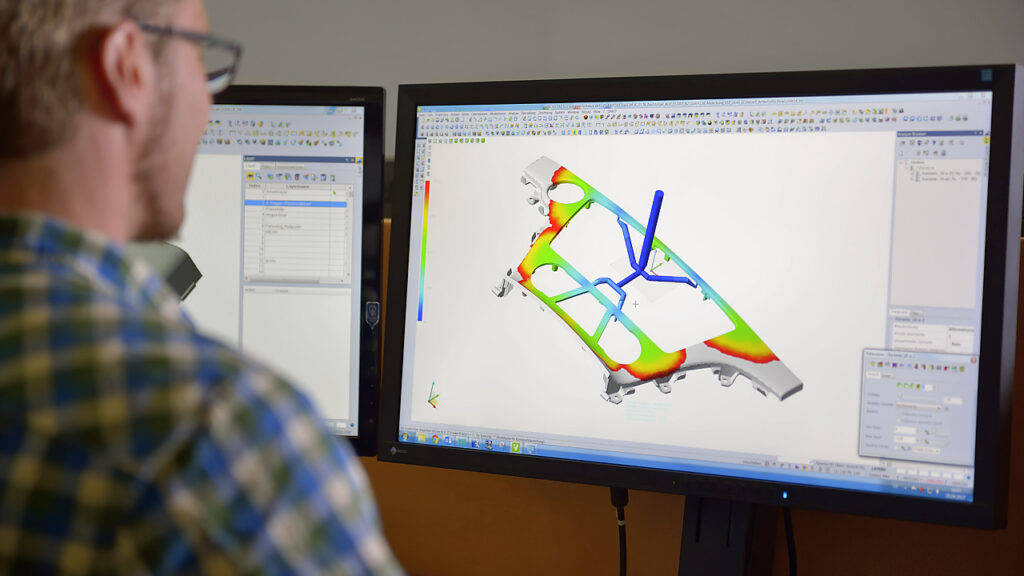
Erstklassige Funktionalität
Einfache Bedienung
Kurze Einarbeitungszeit
Rheologische Analyse für den Konstrukteur
VISI Flow, die Simulationssoftware, ermöglicht dem Anwender aus der gewohnten CAD Umgebung heraus die rheologische Untersuchung komplexer Bauteile. Durch das einfache Bedienkonzept, ist der Aufwand für die Erzeugung der FE Modelle vergleichsweise gering und auch die anschließenden Berechnungszeiten sind im Vergleich sehr kurz. Mit VISI Flow lassen sich schnell alle Phasen des Thermoplastspritzgießens untersuchen. Die Berechnung beginnt mit einer Analyse der Schmelze- und Thermodynamik, um die optimalen Einspritzbedingungen festzulegen und endet mit der Berechnung von Schwindung und Verzug. Da die Ausführungen dieser Berechnungen, die auf der Grundlage komplexer physikalischer Modelle beruhen, vollständig von VISI Flow unterstützt werden, sind keine mathematischen Fähigkeiten erforderlich. Jeder Formteil- und Werkzeugkonstrukteur kann diese Technologie nutzen. VISI Flow simuliert das Verhalten aller Kunststofftypen, sowohl unverstärkt als auch verstärkt. Die Datenbank bietet eine große Auswahl von ca. 6000 Materialien und kann zudem um neue Polymere oder Blends erweitert werden. Es gibt für die Berechnung keine Einschränkungen hinsichtlich Form, Komplexität und Abmessungen der Spritzteile.
Vernetzen und Erstellen eines FE Modells
Die Umwandlung eines Solid Modells von VISI in ein Netzmodell geschieht schnell und vollautomatisch, jedoch immer mit Eingriffsmöglichkeiten des Anwenders der letztendlich entscheidet, zu welchem Detailgrad die Vernetzung erfolgen soll. Die Komplexität der Modellaufbereitung wird stark reduziert, da die berechnungs-relevante Struktur vom System automatisch erzeugt wird. Diese Methode, eine Weiterentwicklung der Shell und Solid Modelle, hat die Besonderheit, die rheologische Simulation einschließlich der Verzugsberechnung zu beschleunigen.
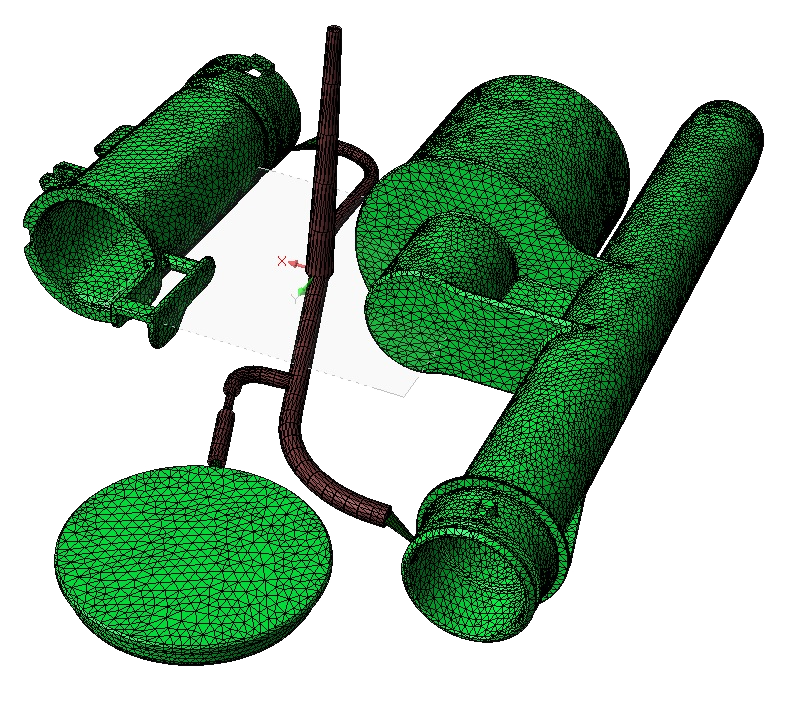
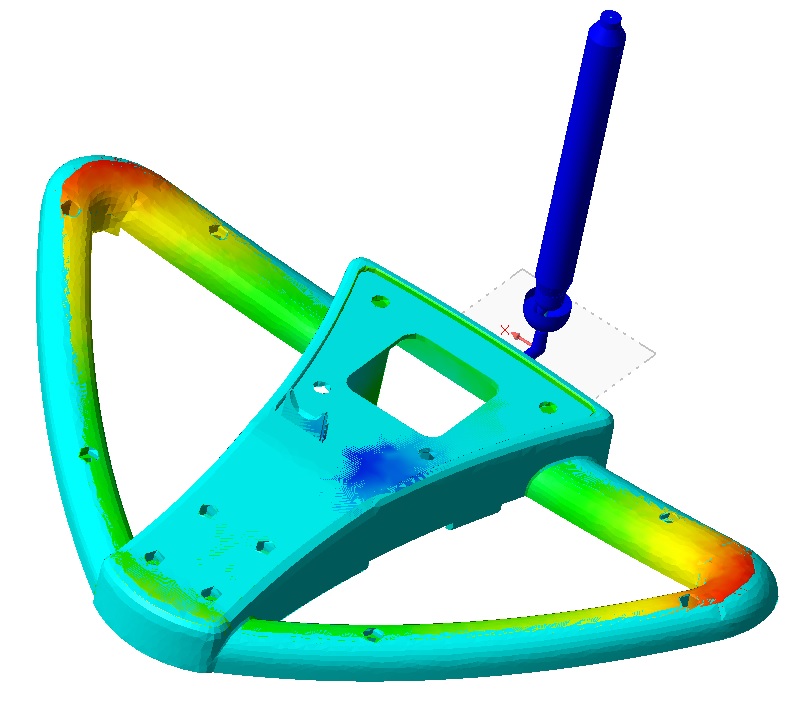
Füllen
Das Basismodul hilft dem Anwender durch die Simulation der Einspritzphase viele Formteilprobleme im Vorfeld zu erkennen und zu vermeiden. Für die Berechnung werden, die Angussgeometrie mit den Anschnittpositionen, sowie die erforderlichen Spritzgießparameter festgelegt. Bei der Simulation kann VISI Flow alle Varianten wie Kaltkanäle, Heißkanäle und innenbeheizte Düsen berechnen. Im Basismodul sind bereits spezielle Optionen für sequentielles (Kaskade) Spritzgießen und für Familienwerkzeuge implementiert, bei denen verschiedene Artikel in einem Werkzeug angeordnet sind und durch unterschiedliches Öffnen und Schließen von Düsen balanciert werden. Im Ergebnis werden neben dem Füllbild auch Temperatur, Scherspannung und mögliche Lufteinschlüsse angezeigt. Auch Bindenähte werden dargestellt, deren Lage bei Bedarf z.B. durch Änderungen am Zuführsystem beeinflusst werden kann. Weiter gibt die Berechnung Aufschluss über den Druckbedarf, sowie die nötige Schließ- oder Zuhaltekraft.
Nachdruck und Verzug
Diese Option erlaubt die Überprüfung des Nachdruckphase und der Kühlzeit um das Risiko von Einsfallstellen zu reduzieren, die Dichteverteilung im Formteil und die volumetrische Schwindung zu kontrollieren. Die Verzugsberechnung rundet den virtuellen Spritzgießvorgang mit der Berechnung des Gleichgewichts aller internen Spannungen am Ende der Zykluszeit ab. Auf diese Weise wird die endgültige Form des Formteils zusammen mit der linearen Schwindung und dem Verzug bestimmt. Das Ergebnis setzt eine homogene Temperierung voraus, die mit der folgenden Option optimiert werden kann.
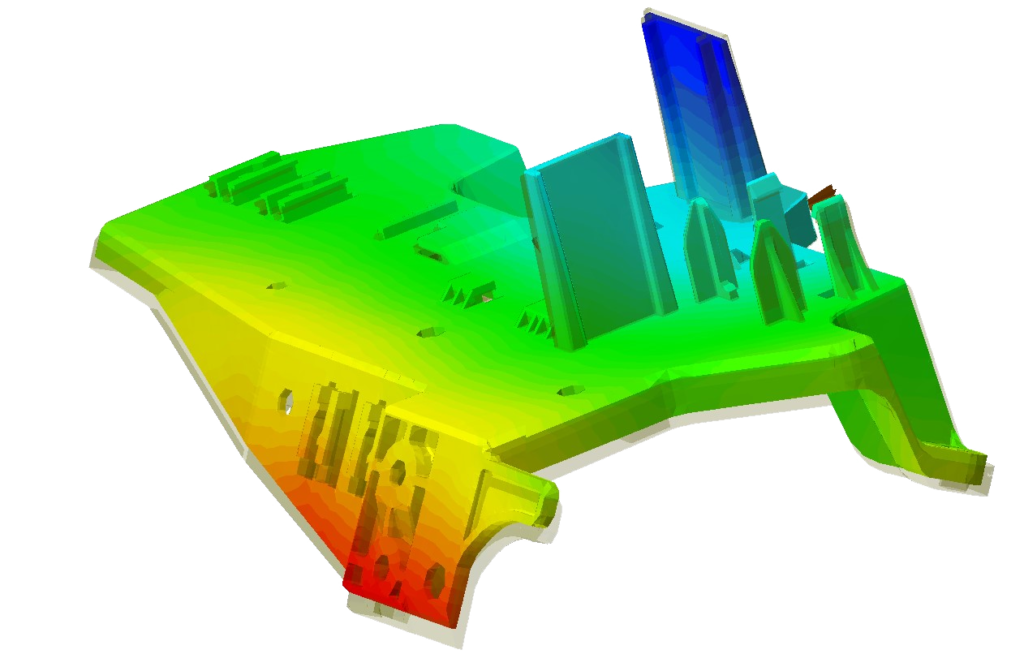
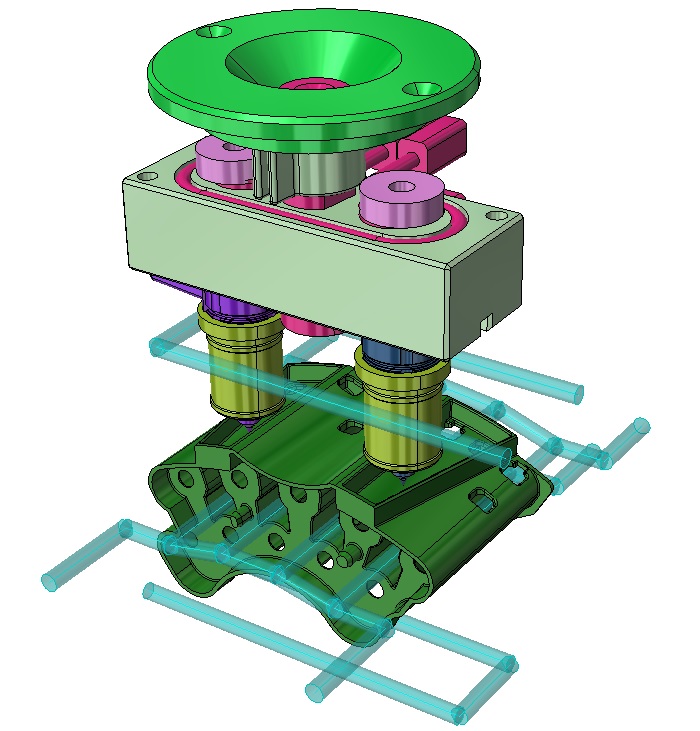
Temperierung
Diese Option erlaubt die Berechnung der Werkzeugtemperierung unter Einbeziehung der vorherigen Phasen. Die auf hohem Niveau, und auf der Basis von Solid Elementen ablaufende Berechnung, erkennt und optimiert die Temperatur des Mediums, der Durchflussmenge und den erforderlichen Druck in jedem einzelnen Kühlkreislauf.
Die Darstellung der Temperaturverteilung in beliebigen Schnitten durch das Werkzeug kann für weitere Optimierungen der Zykluszeit und/oder zur Reduzierung des thermisch beeinflussten Verzuges herangezogen werden. Die Vorteile von Einsätzen oder der allgemeine Gebrauch von hoch wärmeleitenden Materialien für die Werkzeugkavität sind schnell darstellbar.
Overmoulding
Zuerst wird ein Material in die Form eingespritzt, das den Grundkörper bildet. Nachdem dieses ausgehärtet ist, wird das zweite Material in eine zweite Kavität eingespritzt und beide Teile vereinen sich zu einer „Baugruppe“. Das Overmolding Modul unterstützt auch das „Insertmolding“ Verfahren für Einlegeteile. Es wird ein vorgefertigtes Teil (z.B. Blechteil eines Steckers) in die Spritzgussform eingelegt und der Kunststoff wird um das eingelegte Teil gespritzt. Beide Teile gehen dann eine Verbindung miteinander ein. Die Eigenschaften dieser Verbindung sind abhängig von Faktoren wie Bindenähte, Schmelzetemperaturen und der Temperatur der Einsätze während der Verarbeitung.